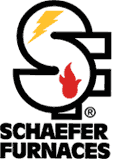
Gas, Oil, or Propane Aluminum Furnaces
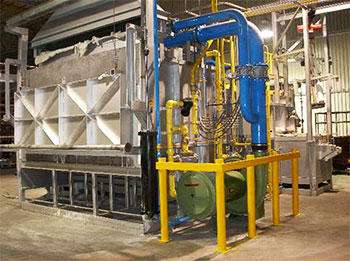
Resources
- Articles
- Brochures
- Presentations
For fuel efficiency like no other; gas, oil or propane aluminum furnaces by The Schaefer Group hit the mark. Typical melting efficiency, based on 100% cold charging with an exterior charge well, is 1,500 BTU of gas per pound (378 kcal/0.4536 kg) of metal in a Schaefer furnace radiant roof-fired reverb. Whatever the fuel, this is only 1,500 BTU per pound (378 kcal/0.4536 kg). And, if you preheat at least 50% of the metal charged in the form of ingot or sows, the number drops to 1,200 BTU of gas per pound (302.4 kcal/0.4536 kg). Batch-type melting reverbs are also available with the latest in high velocity burners.
ADVANTAGES:
- Clean Metal – non-wetting refractory linings will not contaminate the metal.
- Excellent Temperature Control – Filtration is optional.
- Clean Furnace – all blind corners are eliminated and door jambs are tangent with the walls for full accessibility. A clean-out-door provides easy access to the hearth and allows easy clean-up of the furnace bottom or to skim the bath.
- Liquid Metal Deliveries – Schaefer reverbs can be engineered with large holding capacities that offer enough “draw-down” capability to accept molten metal delivery.
- Regeneration & Recuperation (explained under Operation & Maintenance) – improve melting efficiency even more by preheating the ambient air and metal through a combination of pre-heat hearths, regeneration and recuperation. Melt rates of 950-to-1,000 BTU/lb (239.4-to-252 kcal/0.4536 kg) can be obtained with the right combination of equipment.
FOR:
This versatile furnace meets the needs of a variety of metal casters, high and low pressure die casters, permanent mold, sand, investment and lost foam foundries around the world.
OPERATION & MAINTENANCE:
- Low Maintenance – Schaefer furnaces seldom need much attention. Anchored, monolithic linings are custom built to meet specific needs, and all furnace sections are completely accessible for easy maintenance.
- Very high efficiencies – can be achieved by sows and ingot bars, followed by the circulation of molten aluminum in the metal bath. Circulation (stirring) of the entire bath is accomplished by pumping metal through a charge well, followed by:
- Recuperation - combustion air is pre-heated by the flue gases in a non-contact recuperator, resulting in noticeably lower fuel usage – normally up to 15% increase in melting efficiency with 700 degrees Fahrenheit (371 degrees Celsius) pre-heated combustion air.
- Regeneration – cycles the full temperature products of combustion through efficient heat storage beds. Combustion air passing through these beds is raised up to 600 degrees Celsius, delivering 30 to 35% better melting efficiency than with standard radiant roof-fired reverbs. Schaefer was the first aluminum furnace manufacturer to apply this advanced procedure.
Additional Considerations:
- Filtration, degassing, circulation, transfer methods
OPTIONS:
- Circulation wells and molten metal pumps provide rapid heat transfer from the furnace to the pump and charge wells and back again. This is particularly effective when melting chips from machining operations as circulation breaks the surface tension, pulls the chips down into the melt immediately and keeps the bath homogenized. The Schaefer furnace design uniquely minimizes heat loss.